
Society > Together with Employees Occupational Health and Safety
Occupational Health and Safety Management
Based on Environment & Safety Policy, to prevent occupational accidents in the workplace, and promote employee health and a comfortable work environment, the Mitsubishi Tanabe Pharma Group operates management systems in accordance with Guidelines on Occupational Safety and Health Management Systems (OSHMS) presented by the Ministry of Health, Labour and Welfare. In fiscal 2022, Mitsubishi Tanabe Pharma Korea (Hyangnam Plant) acquired ISO 45001 certification, and has been operating in accordance with this certification since then.
The Group conducts regular internal safety audits to verify that safety management, legal compliance, and activities to ensure safety are being conducted in a legal and appropriate manner, working to make improvements while striving to foster awareness of safety through education and training. In safety audits in fiscal 2023, we started again on-site audits of Group companies overseas as the COVID-19 pandemic subsided.
Occupational Health and Safety Promotion System
At Group offices, we have established the Health and Safety Committee, which meets once a month, as a structure for ensuring employee safety and health and creating a comfortable work environment. The committee consists of general health and safety managers (office managers and plant managers), safety managers, health supervisors, occupational physicians, and members selected by the Company and labor union.
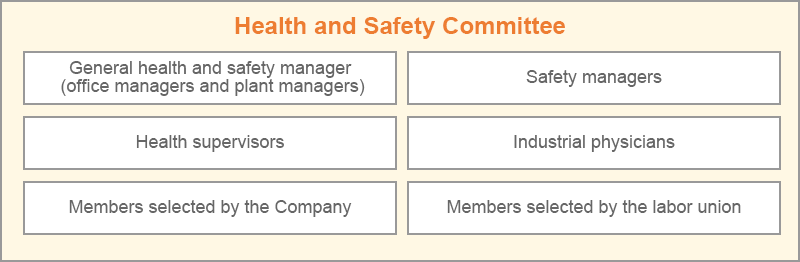
The committee reports on health and safety activities and discusses important policies for preventing occupational accidents and health disorders of employees, and health promotion. The matters reported and discussed by the committee are communicated to all employees through the health and safety meetings held by each division.
Occupational Health and Safety Activities
At the Group, based on the policy stated in our Code of Conduct of prioritizing safety above all else, each office formulates health and safety objectives and implementation plans, and institutes health and safety activities such as hazard recognition training, near-miss reviews, workplace inspections etc., along with periodic risk assessment to identify potential workplace risks and implement measures to alleviate them. Additionally, to prevent work-related accidents, it is important to maintain and strengthen environmental and safety management capabilities, and to enhance the awareness of each employee regarding risk, and we are endeavoring to enhance our on-site capabilities through safety education and training (the ability to solve problems spontaneously and autonomously).
In addition to the Group’s own safety initiatives, we also engaged in shared safety activities as the Mitsubishi Chemical Group, aiming for zero accidents and occupational injuries throughout the Group. In fiscal 2023, as a result of working on a range of safety measures, there were no lost time injuries in our operations in Japan, where we thus achieved our goal of a frequency rate of less than 0.20 lost time injuries. (There was one incidence of a lost time injury overseas.)
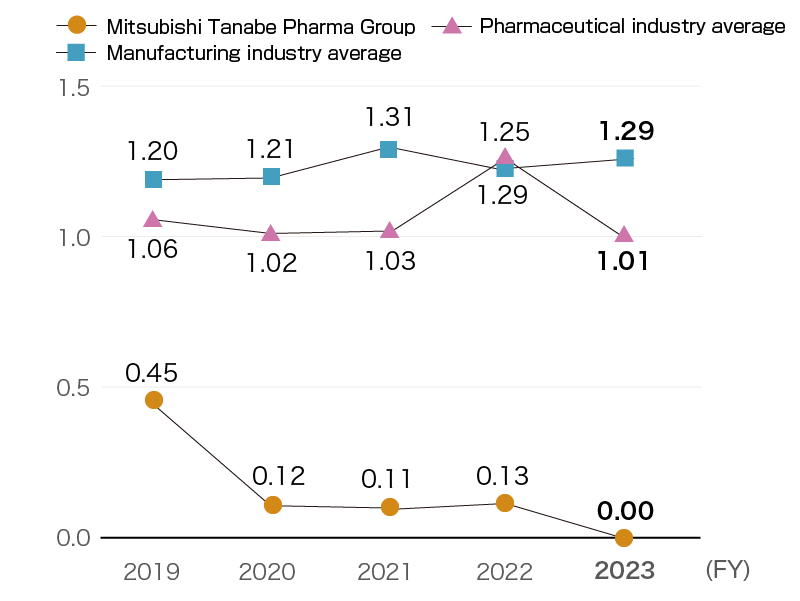
- *Lost time injury frequency rat+M15:P18e:
Number of casualties due to accidents that require time off from work up to one million actual working hours (excluding commuting injuries). - *Calculation period:
For the Group, April to March the next year; for pharmaceutical industry averages and manufacturing industry averages, January to December. - *Scope: All domestic Group offices
- *Total working hours:
Scope has included permanent employees, contract employees (including some part-time employees), and temporary employees. For permanent employees and contract employees calculated as actual work hours; for temporary employees calculated as work hours per day x number of business days x number of employees.
Safety education and training
- Legal/worker compliance obligation training
- Legal/Consideration obligation to safety and health training
- Hazard recognition training
- Human error prevention training
- Risk assessment training (including chemical substances)
- Static electricity training workshop
- Experiential training (fires and explosions, burns/chemical injuries, getting caught in or between equipment, handling of electricity)
- Traffic safety training
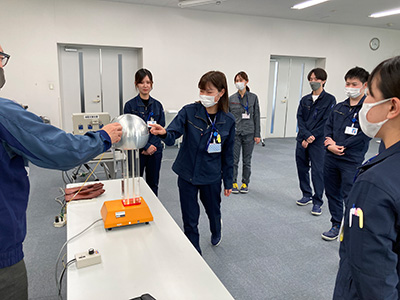
Shared safety activities in the Mitsubishi Chemical Group
- MCG Group Safety Convention (July)
- MCG Group Environment and Safety Awards (August)
- MCG Group Safety Lecture (November)
Chemical Substance Safety Management
As a company that handles many substances, including pharmaceuticals, the Group has established internal regulations related to chemical substances including its Chemical Substance Handling Guidelines, which sets forth the proper handling of those substances.
Accordingly, potential risks are now evaluated in advance (risk evaluation of chemical substances) from the perspectives of both “dangerous and hazardous” and “exposure of people and the environment.” We are taking steps to prevent accidents and disasters related to chemical substances by systematically implementing risk management and mitigation measures from the acquisition of chemical substances to their storage, transport, use and disposal. The Chemical Substances Handling Guidelines also specify measures to prevent or mitigate environmental pollution, accidents, damage to health, fire and explosions caused by hazardous materials. All employees at all offices continue to spread and establish these as guidelines in their ongoing safety, health, and disaster prevention efforts.
Furthermore, we will comply with laws and regulations by conducting education and training on chemical substances as well as safety audits.
In particular, in response to chemical substance regulations based on autonomous management in compliance with the April 2023 revisions to the Industrial Safety and Health Act, the Group provides safety information using Safety Data Sheets and is working to ensure the safety of employees throughout the Group. Measures to this end include appointing personnel responsible for managing chemical substances as well as personnel responsible for the wearing of protective equipment, and conducting operations and management in compliance with rules and regulations.
Safety and Accident Prevention
To prevent safety-related accidents, the Group identifies risks at each office, prioritizing them and examining measures for their removal or reduction, and then reflecting them in the capital investment plan for the next fiscal year to improve unsafe facilities and equipment. Moreover we actively promote operation-specific training in handling of low voltages, and are working to ensure employee safety and improve electrical safety.
Additionally, we use safety assessments and horizontal application of near-miss reviews to implement safety measures required in dangerous locations and to prevent accidents and disasters before they occur.
Employee Survey
Since fiscal 2011, the Mitsubishi Tanabe Pharma Group has implemented employee surveys at domestic Group companies to provide a comprehensive understanding of employee attitudes toward their jobs and of the Company’s workplace health and safety environments in order to improve management initiatives. From fiscal 2019 we expanded the scope of these initiatives to include overseas Group companies.
As a result of efforts in fiscal 2023, we have on the whole maintained a good work environment and employee vitality. Based on some of the issues that have been found to increase engagement, we are promoting dialog between management and employees, as well as initiatives at each division.
Together with Patients and Healthcare Professionals
- Research & Development
- Stable Supply
- Manufacturing Pharmaceuticals that are Secure, Safe, and Convenient to Use
- Information Provision
- Drug Safety / Quality Assurance
- Solving Issues Related to Improving Access to Healthcare
Together with Employees
- Human Resources Development
- Promoting Diversity & Inclusion
- Work-Style Innovation
- Occupational Health and Safety
- Health and Productivity Management